Metal Injection Molding
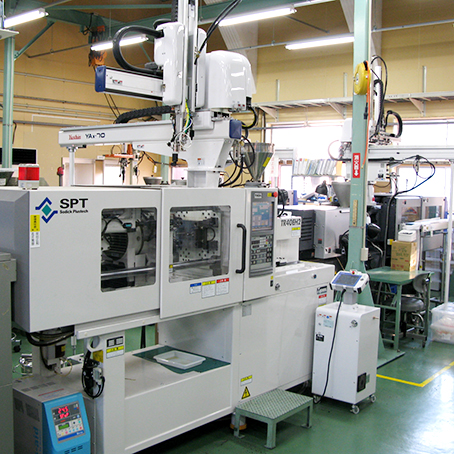
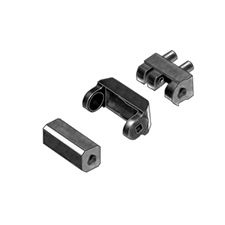
Metal injection molding (MIM) is a state-of-the-art metalworking technique that efficiently manufactures small, metallic parts of complex shapes. Productivity can be improved markedly using MIM technology, and small, metallic parts that have traditionally been produced using a precise lathe, machining, precision casting, and other steps, can now be manufactured in volume. In MIM, metal powder and special plastic are mixed, and the result is then molded, before being processed in the furnace with degreasing and sintering to produce a metal part. The process draws on elements of the plastic injection mold technologies and molding techniques. Kikuchi has developed MIM by harnessing the technologies it has developed out of its experience with diverse processing methods.
MIM technology is now being used by other companies, but Kikuchi remains distinct given the original technology it uses in the sintering process. We can also offer an MIM parts production service, integrated with our package solution system that encompasses all stages from an order for a metal cutting part prototype, to experimental metal molding and volume production of the part produced by MIM. Operations in experimental mold and volume production are part of the Kikuchi Group, with the mission of enabling a smoother start to volume production through a relationship between the Group’s experimental mold business and customer R&D sections, ultimately contributing to faster launches of new products.
Plastic Injection Molding
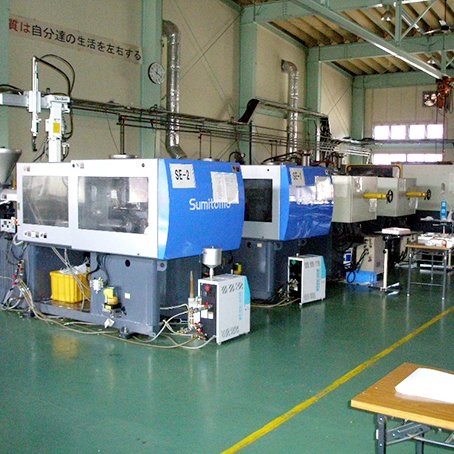
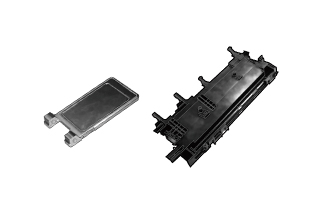
Kikuchi’s original block build method is an injection molding technology that considers the material (resin) specification, and aims to achieve greater accuracy, shorter turnaround times, and reduced costs in processing involving experimental parts, small quantities of limited production goods, and volume production. In plastic molding, Kikuchi can handle injection mold requirements ranging from 50 to 1000 tons, with mold materials such as NAK (pre-hardened steel), aluminum, brass, and cast iron (or composites). We can also deal with large parts of up to 350 tons in Japan and up to 1000 tons at KOREA Kikuchi. We can also assist customers throughout the experimental part production process, by tapping the technologies of our Group companies in aspects such as the joint between plastic and metal parts, mold tool production, and molding (insert mold and block build mold).
Magnesium Thxio Molding
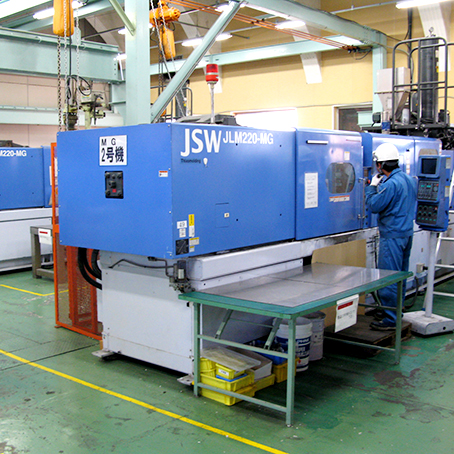
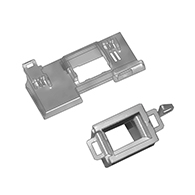
Magnesium has found growing application in recent years, in products such as single-lens reflex digital cameras, cell phones, and notebook computers, because it is lightweight yet stronger than plastic, and is less expensive than titanium. This growth has, however, been hindered by the fact the magnesium molding is difficult, and the processing equipment is very expensive. Kikuchi has developed impressive know-how in this area, as one of the first companies to realize the potential of magnesium and to introduce a magnesium molding machine, in 1998. Consequently, we can now offer an excellent thixo molding method for mass production, and respond to customer needs for limited trial production, small runs for development introduction, and then full volume production. With this capability, we have begun to attract attention from an entirely new range of industry sectors.
Insert Molding
Insert molding is an industrial technique that derives from plastic injection molding, and is a technology used to make integrated component modules by loading the insert goods (mainly sheet metal) into the metal mold and filling with resin. Subsequent processes such as assembly can be omitted, integrating all finished parts in the molding process and streamlining production. Moreover, by loading two or more insert goods (sheet metals), a complex, exact integral molded piece can be obtained. Excellent resin insulation and metal electric conductivity are combined, so insert molding is used in particular for parts for electronic equipment.
Cleanroom molding
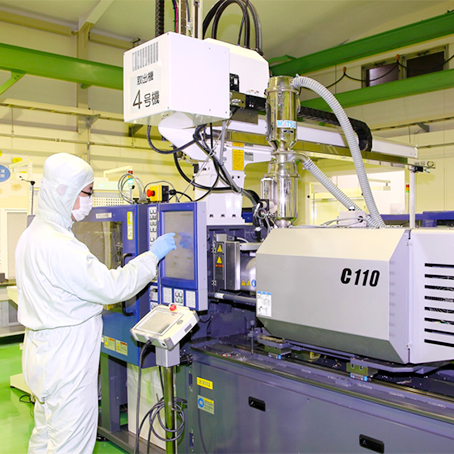
Cleanrooms require high levels of air cleanliness (measured by the number of dust particles floating in the air) and microorganism cleanliness. Such rooms are used in a wide variety of industrial processes, including production processes of semiconductors, LCDs and other electronic components, printing process, and in the manufacturing of printed circuit boards, lenses, and optical equipment). Cleanrooms are also used to prevent contamination in pharmaceutical and food production processes and for biotechnology research healthcare.
Having obtained certifications of CLASS 8 of the JIS B 9920 standard, CLASS 8 of the ISO 14644-1 standard, and CLASS 100000 of the FED-STD-209E standard, Kikuchi Seisakusho has a track record of producing precision machine parts and medical products.
Alminium hot diecast
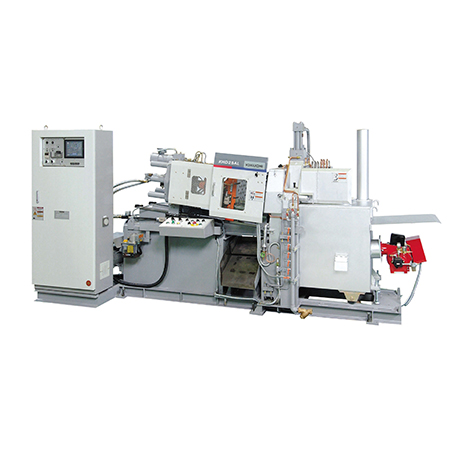
An aluminum hot chamber is a forming technology that makes possible complex forms, such as plastic injection molding. As it injects into high-temperature molten metal, melted aluminum alloy can be cast directly into the mold.
The efficient production of aluminum casting, traditionally hard to achieve with the hot chamber process, is now enabled with our original technology and know-how.
Thin-wall thickness of 0.3 mm is available and dimension tolerance ±0.05mm is possible.
Injections are done in molten metal, minimizing air and gas bubbles and enabling high strength molded parts.
Moreover, pure aluminum can be processed by the hot chamber process.
Because the injection is done at low pressure, tool life is longer than it is with the conventional cold chamber process, which is another feature of the hot chamber process.
Kikuchi will strive to respond to customer needs by developing products that cannot be processed by the conventional cold chamber, forging and extrusion processes, and developing prototypes using special aluminum alloys.