A large variation of the latest equipment leads to the realization of the optimal process in the shortest lead time.
This supports the “package solution system” of Kikuchi.
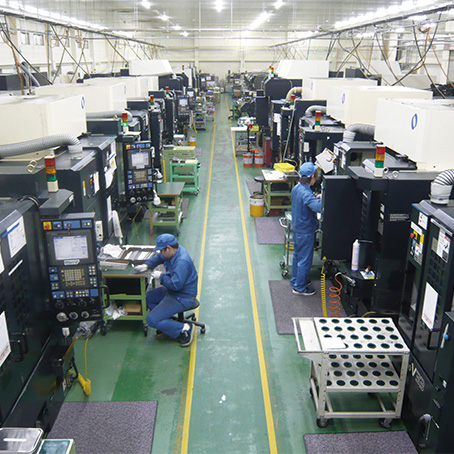
Kikuchi backs up the optimized monozukuri of customers with the maximum level of resources.
We are equipped with a large variation of the state-of-the-art equipment, with more than 400 machines of 200 different types installed in our 15 domestic and overseas manufacturing locations.
We are raising the value of being a company that provides integrated support for monozukuri by helping companies operate a new form of monozukuri.
Through a solid production foundation equipped with state-ofthe-art equipment, Kikuchi realizes speedy prototyping and mass production that is attuned to the challenges faced by customers.
Each manufacturing location cooperates with the development and design department of the Head Office and shares CAD/CAM data online, in order to conduct processing, evaluation and mass production in real time.
The state-of-the-art equipment is on the same level in terms of quality and production volume as each specialized manufacturer and adapts to a wide range of domains from tool & die manufacturing, various types of molding and processing, sheet-metal press processing, machining to equipment design.
Therefore, it supports the “Monozukuri that contributes to monozukuri” of Kikuchi.
Artisan’s skill:Precise sheet-metal processing.
We provide precision processing at a thickness of 50 μm and a precision of 30 μm with a short lead time, which enables the processing of a wide range of materials from very small precision articles to large sheet metal. We have a lineup of various fine laser processing machines, press brakes from 25 to 60 tons, and more than 20 press machines from 18 tons to a maximum of 300 tons. We also offer servo presses that can conduct drawn processing at a maximum of 50 mm.
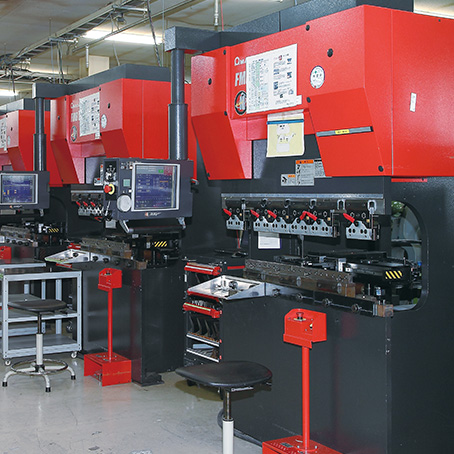
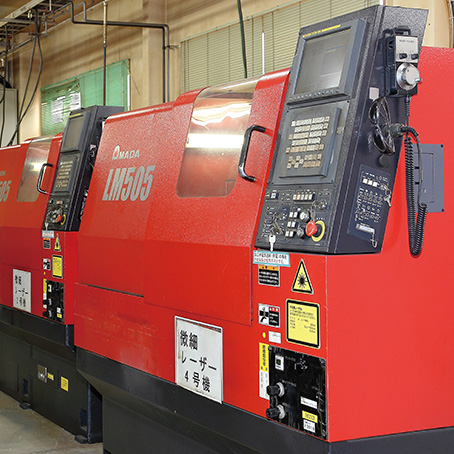
Cutting and processing that shape a diverse range of things
We process a diverse range of materials.
We have many different types of processing equipment.
In the entire company, there are more than 100 machining centers, with about 20 that can respond to 5-axis machining.
Through the smallest tool diameter of 50 μm, the ultraprecise processing machine (IQ300) can process at a processing precision of 5 μm and below.
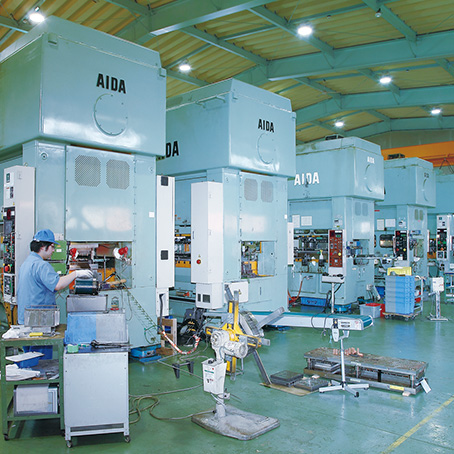
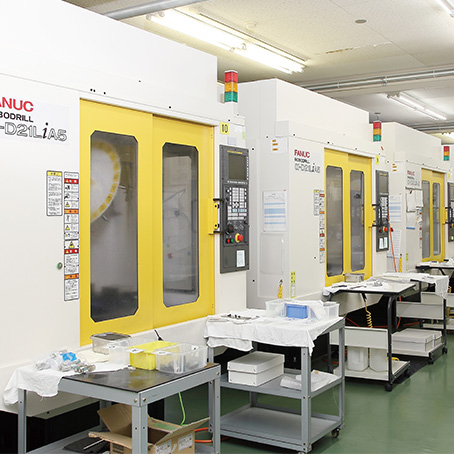
Providing added value by accepting orders for materials that are challenging to mold or cast
For MIM, which enables the processing of various materials including SUS, iron and zinc, we have 11 molding machines from 25 to 75 tons, as well as 8 vacuum sintering furnaces that condense our original know-how. For MG molding (thixo molding), we have 4 molding machines from 75 to 220 tons, which can be used for various components from exterior to miniature interior components. For HC, which can conduct casting at an injection pressure that is one-third of the usual hot chamber method, we are equipped with 12 machines from 15 to 50 tons, which enables the casting of DMS series high-concentration aluminum.
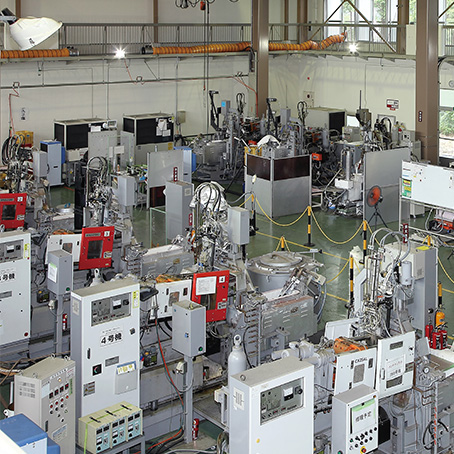
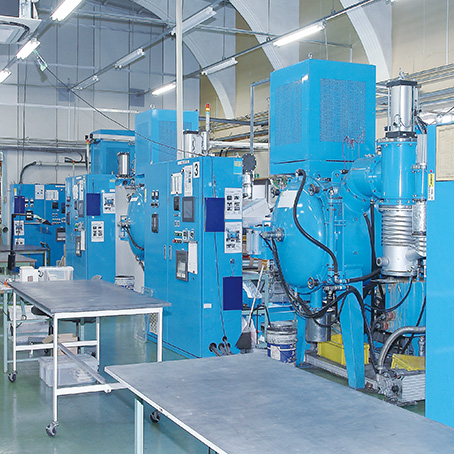
Molding processing that realizes a short lead time through unified handling
We handle the processes of design, tool & die processing and molding in a unified manner. We have a lineup of more than 30 molding machines from 50 to 350 tons, which can handle special molding such as insert molding, multicolor molding and long carbon fibers. For cleanroom molding, Kikuchi is also complete with class 8 (100,000 and below) medical device-related and food-related equipment.
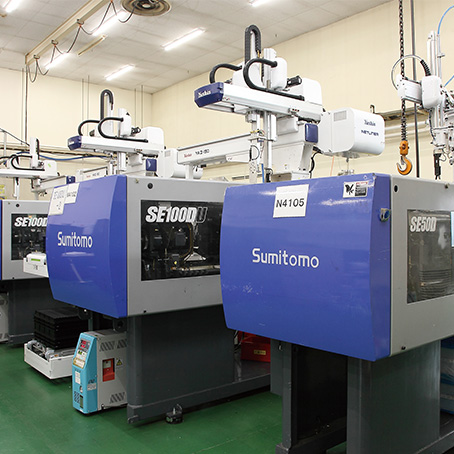
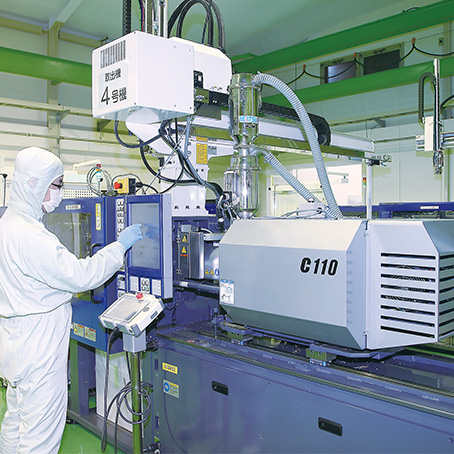